Компонентами гипсобетона являются гипс, песок и опилки, перемешанные с водой и замедлителем схватывания гипса. Крупноразмерные плиты из гипсобетона изготовляют шириной до 3050 мм и длиной до 6000 мм. Учитывая пониженное сцепление гипсобетона со стальной арматурой вследствие его расширения (на 0,2—0,8 %) при твердении, для повышения прочности гипсобетонные панели армируют деревянными рейками. Гипсобетонные изделия обладают такими свойствами, как малая плотность, несгораемость, высокое звукопоглощение и др. Крупноразмерные гипсобетонные плиты изготовляют методом проката. Хранящиеся в силосном складе 1 (рис. 7.16) гипсовые вяжущие материалы по мере необходимости пополняют расходные бункера 2 вяжущих. В дозировочном отделении имеются также расходные бункера 4 опилок и бункера 3 песка. В расходные бункера песок и опилки поступают соответственно из приемных бункеров 6 и 5. Компоненты перемешиваются в две стадии: первая стадия — сухое перемешивание — в приемном лотке, одновременно транспортирующем сухую смесь; вторая стадия — с водой и замедлителем схватывания — в гипсобетоносмесителе непрерывного действия. На прокатном стане 11 гипсобетонной смесью заполняют реечные каркасы, предварительно подготовленные на посту 7 и уложенные на резиновую ленту нижнего транспортера. Гипсобетонная масса, распределенная по нижней ленте и уплотняемая резиновой лентой верхнего конвейера, проходит через щель между прокатными валками и формируется до заданной толщины. Скорость лент верхнего и нижнего конвейера 32—97 м/ч. Процесс формования на прокатном стане заканчивается калибровкой панелей между верхним и нижним блоками калибровочных валков. Рис. 7.16. Технологическая схема производства гипсобетонных панелей методом проката Скорость движения ленты конвейера обеспечивает прохождение панели через прокатный стан за 15—20 мин. За это время гипсобетонная смесь схватывается и приобретает прочность, равную 15—20 МПа. Далее панель поступает на обгонный роликовый конвейер 10, который разделяет панели и поочередно передает их на кантователь. Затем панели устанавливаются на кассетную вагонетку 9 и направляются в прямоточные тоннельные сушила 8 с теплоносителем температурой 378—408 К. Продолжительность сушки панели 18—24 ч. Структурная схема установки изображена на рис. 7.17. Смеситель 1 представляет собой горизонтальный цилиндр, внутри которого вращается лопастной вал 2. Сухие компоненты вводятся через загрузочную горловину 35, а готовая смесь выдается через воронку 3. Специальное устройство 34 обеспечивает равномерное распределение гипсобетонной смеси по ширине ленты прокатного стана. Прокатный стан 1 состоит из привода, рабочей и накрывной лент, шнека для сбора отходов, устройств для мокрой очистки лент, калибрующей и приемной секций. На прокатном стане осуществляется укладка деревянных каркасов, распределение смеси и формование гипсобетона. Привод стана обеспечивает движение рабочей 6 и накрывной 33 лент с одинаковой скоростью в пределах 60—120 м/ч. Привод состоит из электродвигателя 28, тахогенератора 27, редукторов 30 и цепной передачи 29 на вал приводного барабана 14 рабочей ленты. От вала приводного барабана 14 через систему передач 11 и 12 крутящий момент передается на вал приводного барабана 31 накрывной ленты 33, имеющей равную с рабочей лентой скорость. Под приводным барабаном 14 рабочей ленты смонтировано устройство для сухой очистки ленты, представляющее собой вал 1Ь с лопастями, вращающийся от автономного привода 13. Аналогичное устройство имеется под накрывной лентой, а также у лент обгонного роликового конвейера 2 и кантователя. Шнек 16, установленный под приводным барабаном 14, предназначен для сбора отходов и измельчения с последующей их утилизацией путем возврата в гипсобетоносмеситель 1 конвейерами 28 и 32. Рабочая и накрывная ленты имеют также устройства для мокрой очистки, представляющие собой каретку 10 со щетками, совершающими возвратно-поступательное движение. Загрязненные стоки из очистных устройств поступают в специальные сборники. Вибробалка 7 предназначена для лучшего распределения смеси по ширине ленты и уплотнения ее. Калибрующий барабан 8 обеспечивает первичную калибровку панели. С помощью специальных винтов расположение барабана можно изменять по вертикали, чем достигают требуемой толщины панели. Окончательная калиброЁка панелей по высоте обеспечивается обжимными роликовыми обоймами 9, положение которых по вертикали изменяют специальными винтами. Приемная секция предназначена для передачи деревянного каркаса панели на ленту прокатного стана. Она состоит из натяжного барабана 4, рабочей ленты и шнека 5 для очистки внутренней поверхности ленты.
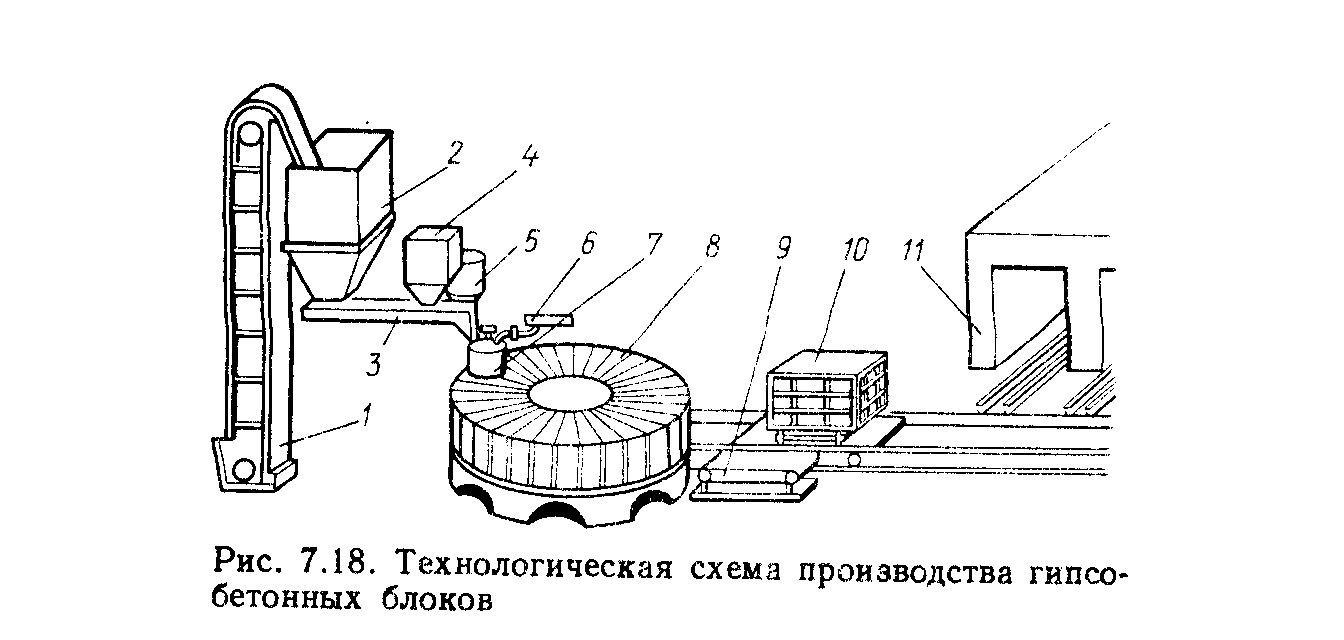
- Перечислите основные гипсовые изделия, их область применения.
- Укажите основные этапы производства сухой гипсовой штукатурки.
- Для чего предназначены формующий стол, насыщающий конвейер, конвейерная сушилка. Опишите их конструктивные особенности.
- Опишите метод изготовления пустотелых гипсовых плит.
- Опишите технологию для изготовления гипсобетонных плит методом проката и оборудование для его изготовления.
11.03.2015 110.59 Кб 7 ОБЩЕСТВО.DOC
Бизнес идея производство 3D панелей из гипса. Изготовление 3д панелей Идеи для бизнеса Бизнес с нуля
Производство гипсовой плитки как бизнес с нуля в 2022
Ограничение
Для продолжения скачивания необходимо пройти капчу:
Источник: studfile.net
Производства 3D панелей своими руками.
Почему это выгодно? Вопрос закономерный и очень правильный! Объясняем. Во-первых, не требуется создавать какие-то особенные условия. Более того, вам не нужны большие помещения.
Минимальные габариты – всего десять квадратных метров. Вы покупаете готовые формы, мы предоставляем вам полный набор обучающих материалов, включая видео. После их изучения вы сможете начать работу. Никакого специального обучения не требуется.
Фактически, с этого момента вы вкладываете деньги исключительно в закупку сырья – гипса, или других строительных смесей.
Эти материалы производятся на территории нашей страны и стоят недорого. В среднем, гипс обойдётся рублей четыреста за упаковку весом тридцать килограммов. Из такого количества сырья можно получить до двух квадратных метров готовой продукции.
Если вы поставите разумные цены, то есть прекрасная возможность развить это направление в вашем регионе и стать лидером. А в будущем – расшириться далеко за пределы своего города и области. Благодаря таким инициативам у 3D-панелей есть отличный шанс войти в число наиболее популярных материалов для отделки.
Вы быстро оцените преимущества. Ведь уже с первого заказа ваше оборудование и формы начинают окупаться, благодаря небольшим затратам.
Формы
Второе дыхание. Проект ООО НПО «ELXOLDING» по производству строительных блоков из гипсовых вяжущих
История НПО «ELXOLDING» уходит корнями в далекие 1980-е годы, когда в Самарканде был образован производственный кооператив «Буран». После 1991 года — с наступлением новой эпохи в экономике страны — кооператив активно развивался: в его структуру влились другие предприятия, а спектр направлений деятельности значительно вырос.
В 2006 году все активы были объединены под крылом новой организации — ООО «Научно-производственное объединение «ELXOLDING». За несколько десятилетий присутствия на рынке компанией было задумано и реализовано множество инновационных и инвестиционных проектов. Некоторые из идей и начинаний, в свое время не получивших логического продолжения, в сегодняшних рыночных условиях вновь приобрели особую актуальность и востребованность. Один из самых перспективных таких проектов — производство блоков для строительства жилых помещений из гипсовых вяжущих различных марок.
Назад — в будущее строительной отрасли
В настоящее время ООО НПО «ELXOLDING» специализируется в основном на производстве учебно-лабораторного оборудования для учебных заведений различного уровня, грузовых трехколесных мотоциклов, прицепов для легковых автомобилей и сельскохозяйственной техники. Однако в 1990-е годы — на начальных этапах своей истории — его деятельность была связана в первую очередь с созданием и внедрением новых технологий для строительной, химической и медицинской отраслей. Предприятие активно работало в области производства стройматериалов, мини-установок для производства карбида кальция и переработки аккумуляторного лома, медицинского оборудования, в частности анализатора глюкозы и др.
Именно тогда — в 1991–1993 годах — была начата реализация проекта по производству строительных блоков из гипсовых вяжущих различных марок, предназначенных для строительства жилых помещений. В 2018 году, спустя без малого 30 лет, этот проект вновь обретает актуальность.
Сегодня строительная отрасль переживает значительные изменения, связанные с ужесточением требований к экологической безопасности, ресурсосбережению и энергетической эффективности процессов и объектов строительства.
Так, с целью экономии энергии в сфере ЖКХ на государственном уровне разрабатываются и реализуются различные программы — среди них стоит особенно выделить программы «по строительству доступных жилых домов по обновленным типовым проектам в сельской местности на 2017–2021 годы» от 21.10.2016 г. и «О мерах по коренному совершенствованию деятельности Государственного комитета Республики Узбекистан по архитектуре и строительстве». Кроме того, Указом президента № УП-5030 от 01.05.2017г. определено внедрение в строительное производство передовых технологий, обеспечивающих снижение стоимости строительства и рациональное использование ресурсов.
Для решения поставленных государством задач необходимо разработать проекты энергоэффективных жилых зданий, простых и дешевых в эксплуатации, а также организовать производство долговечных недорогих материалов для их строительства.
Такие материалы должны по своим качественным характеристикам, конструктивным и теплофизическим свойствам ни в чем не уступать или даже превосходить традиционные (кирпич, блоки из ячеистого бетона, панели, монолитный бетон и т. д.), а также отвечать новым требованиям в области экологической безопасности, энерго- и ресурсосбережения — в идеале, при их производстве должно использоваться только местное сырье и отходы различных производств.
Гипсовые материалы в полной мере отвечают всем этим требованиям. Их применение позволяет не только снизить дефицит стеновых материалов, но во многих случаях заменить энергоемкие цементные вяжущие без какого-либо ухудшения эксплуатационных свойств, а также значительно (не менее чем в два раза) сократить сроки возведения зданий.
Предпосылками к этому служат высокая эффективность переработки повсеместно распространенного в Узбекистане природного гипсового сырья и гипсосодержащих отходов в гипсовые вяжущие; простота производства изделий из них (преимущественно без тепловой обработки), а также высокие качественные показатели — малые тепло- и звукопроводимость, огнестойкость, высокая декоративность и комфортность, экологическая безопасность.
Гипс — строительный материал XXI века
В последние годы применение гипсового вяжущего на единицу объема строительных работ выросло во многих развитых странах мира: в одной только Японии и США – в 1,8 и 2,5 раза соответственно.
Всеобщий интерес к гипсовым строительным материалам вызван прежде всего простотой и экономичностью их производства. К примеру, на производство одной тонны гипса требуется почти вчетверо меньше топливно-энергетических ресурсов, чем на производство тонны цемента. При прочих равных условиях строительные материалы и конструкции, изготовленные с применением гипсового вяжущего, выгодно отличаются от материалов, изготовленных с применением вяжущих других видов.
Преимущества гипсовых блоков:
1. Экологичность. Основной компонент гипсовых блоков — гипс — экологически чистый природный материал.
2. Пожаробезопасность. Гипс – негорючий материал, и изделия на его основе сохраняют это свойство. Гипсовые блоки могут в течение трех часов выдерживать температуру до +1100°.
3. Хорошая звуко- и теплоизоляция. Уровень теплоизоляции гипсового блока толщиной в 80 мм равен уровню теплоизоляции стены из бетона толщиной в 400 мм.
4. Простота в обращении. Возведение перегородок вполне по силам одному человеку: масса одного квадратного метра перегородки из полнотелых блоков — 82 кг, из пустотелых блоков — 67 кг. Для обработки гипсовых блоков не нужны специальные инструменты и приспособления. А еще перегородки из гипсовых блоков не требуют выравнивания, поэтому чтобы оклеить перегородку обоями, ее достаточно просто прогрунтовать.
5. Улучшение микроклимата. Гипсовые блоки могут впитывать лишнюю влагу и, наоборот, увлажнять воздух.
6. Долговечность. Гипсовые блоки не подвержены воздействию гнили.
7. Универсальность. Гипсовые стеновые блоки можно активно использовать как в гражданском, так и в промышленном строительстве для разработки внутренних и внешних стеновых конструкций.
Кроме того, гипсобетонные перегородки значительно выгоднее кирпичных (на 25–35%), железобетонных (на 10–15 %), фибролитовых и деревянных щитовых (на 40–50%).
Преимущества гипса в качестве материала для внутренних стен и перегородок не вызывают сомнений, однако в условиях Узбекистана гипсовые блоки могут с успехом применяться и при возведении внешних стен особенно в малоэтажном строительстве. Климат республики достаточно жаркий, сухой, осадки сравнительно нечасты, поэтому сооружения из гипсовых блоков стоят долго и практически не разрушаются со временем.
В качестве примера можно привести два двухэтажных здания в Самарканде, которые построены в 1992 году из гипсовых блоков, произведенных НПО «ELXOLDING». Одно из зданий было оштукатурено песчано-цементной смесью, второе — не было перекрыто и не эксплуатировалось. Спустя 26 лет кладка из гипсоблоков полностью сохранилась, в недостроенном здании под воздействием атмосферных явлений и осадков гипсовые блоки приобрели желтовато-серый оттенок, но признаков разрушения нет.
— Наш проект направлен на производство технологического оборудования для выпуска гипсовых блоков в объеме 4200 м2 гипсовых материалов в месяц. Стоимость оборудования в зависимости от выбранной комплектации с учетом транспортировки во все регионы республики, монтажа, пуско-наладочных работ и прочих издержек составляет от 306 тысяч долларов США. Наличие действующих производственных мощностей и всей необходимой инфраструктуры позволяет производить до 10 комплектов оборудования в месяц при организации одной рабочей смены. Чистая прибыль от каждого комплекта оборудования составляет 10–20%. Председатель наблюдательного совета Дониш Шукуров
Производство гипсовых блоков — перспективный бизнес
Рост темпов капитального и индивидуального жилищного строительства в городах и сельской местности свидетельствует о том, что потребность в гипсовых материалах в долгосрочной перспективе будет только расти, поэтому производство гипсовых блоков остается крайне востребованным направлением деятельности.
Перспективно оно и с точки зрения еще одного важнейшего показателя — уровня себестоимости продукции. Себестоимость гипсовых блоков очень невысока. Этому способствует множество факторов.
Во-первых, важную роль играет развитая сырьевая база: на территории Республики Узбекистан более 25 крупных месторождений гипса, так что производитель имеет возможность использовать местное сырье и существенно сократить расходы на его транспортировку. Наиболее целесообразно расположить завод по производству гипсовых блоков рядом с заводом по производству гипса. Это позволит иметь меньший запас сырья на заводском складе и использовать гипс более высокого качества. Правильное хранение и расходование других составляющих материалов также позитивно скажется на сокращении издержек.
Другим фактором, определяющим снижение себестоимости производства, является применение энерго- и ресурсосберегающих технологий, предполагающих минимально возможный расход тепловой и электрической энергии. Особенно важно отметить, что львиная доля энергии при производстве гипсовых блоков — до 30%! — расходуется на сушку, однако в климатических условиях Узбекистана при среднегодовой температуре + 15 °С, средней летней + 36 °С, эти расходы уменьшаются более чем в два раза.
И наконец, третий немаловажный фактор, определяющий объем издержек в производстве гипсовых блоков – тип применяемого оборудования. Наилучшее решение — применение высокопроизводительных карусельных машин.
Гипсовые стеновые блоки — экологически чистый и безопасный материал, одобренный всеми экологическими комиссиями. Поэтому несмотря на то, что производство гипсовых блоков осуществляется при непосредственном и постоянном контакте с человеком, гипс не оказывает негативного воздействия на кожу и органы дыхания работников.
В настоящее время в Республики Узбекистан гипс в основном используется в отделочных работах, производстве гипсокартона и шпаклевок, а вот штучные гипсовые строительные материалы пока не получили широкого распространения — как раз по причине отсутствия современного технологического оборудования.
Высокие темпы капитального строительства, а также индивидуального жилищного строительства в городах и сельской местности дают уверенность в том, что данный проект при относительно небольших инвестициях может приобрести второе дыхание.
Источник: glavportal.com